Planning Certificate - APICS
E-Learning

DURATION
20 hours

PRICING
Contact us for the price of the course and to subscribe.
ASCM’s Supply Chain Planning Certificate program introduces these essential planning fundamentals and clearly explains how to integrate all planning functions within a company.
The self-paced, online program includes 20 hours of education and a comprehensive final exam. After passing the exam, learners will receive a certificate and digital badge.
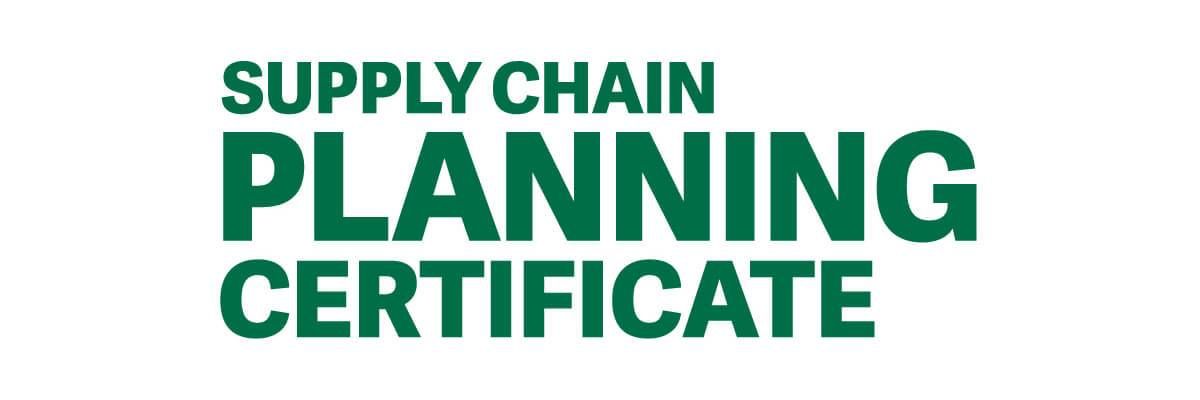
The program helps your team to develop a common language and knowledge base while exploring how to:
- Trace the flow of planning from business plan to execution
- Understand and manage the master production schedule
- Understand and manage the material requirements plan
- Help advance supply and operations planning meetings
- Identify technologies to support synchronous planning
- Create a channel tree design for a distribution system
- Contribute to production activity control activities
-
Teaching plan
READ THE DETAILS ▾
DETAILED PROGRAMME
1. What Is Synchronized Planning?
Planning
Why Do Companies Plan?
How Do Companies Plan?
Manufacturing Planning and Control (MPC) System
MPC Overview
Strategic Planning
Operations Management Planning
Operations Execution
Distribution Planning
Technologies within Strategic Planning
What Is Synchronized Planning?
Synchronized Planning Definition
Digital Capabilities Model (DCM)
Why Synchronized Planning?
Level 1 Capabilities
Level 2 Capabilities
Additional Digital Information Technology for Supply Chains
Technologies within the Digital Supply Chain2. Strategic Planning – Business Planning
Market and Technology Variables in Business Planning
Current and Evolving Environments
Industry Advances and Technological Evolution
Digital DevelopmentSynchronized Business Planning Hierarchy
Introduction to the Planning Hierarchy
Synchronizing the Mission – Getting Everyone on the Same Page
Synchronizing the Vision – Keeping Everyone on the Same Page
Strategic Plans – Balanced Scorecard
Strategic Plans – Channel Network and Scenario Planning
Synchronizing Financial Planning and Growth Strategy
Financial Planning – Profit and Loss Statements
Financial Planning – Sales and General Administrative Expenses
Business Imperatives – Synchronizing Resources with Objectives
Functional Support – Synchronizing Recourses with Objectives
Synchronizing Core Process with Strategic Planning ObjectivesOther Tools and Techniques to Support Synchronized Business Planning
Hoshin Kanri - Vertical and Cross Functional Alignment of Objectives
Portfolio Life Cycle Planning–Synchronizing Plans with Product Life Cycles
The ASCM Sustainability Framework
Operations Strategy – Manufacturing Environments
Operations Strategy – Inventory Planning
Supply Chain Strategies
Synchronizing Strategy for Multiple Business Units (in Larger Businesses)3. Strategic Planning – Demand Planning and S&OP
Demand Planning
Misguided Assumptions
Synchronizing with Business Planning
Business Plan Objectives
Marketing Investments
Sales Management
Historical Time - Series Data
Digital Contract ManagementSales and Operations Planning (S&OP)
S&OP Overview
Prerequisite Activities and Data Gathering
Key Measurements
Scheduling the Monthly S&OP Cycle and Steps
Software and Product Line Templates
S&OP Cycle and Final Meeting Agenda
Roles and Responsibilities in S&OP
Tiered S&OP
S&OP Handoff to the Organization4. Tactical Planning – Master Scheduling/MRP/Capacity Management
Master Scheduling Overview
Objectives of Master Scheduling
Relationship of Master Scheduling to Other Plans
Differences in Master Scheduling based on Manufacturing Strategy/Business Environments
Inputs to the MPSThe Master Scheduling Process
The MPS Grid
Steps in the Master Scheduling Process
Managing Change and the MPSMaterial Requirements Planning Overview
Objectives of MRP
Relationship of MRP to Other Plans
Inputs to MRP
Bills of Material
Types of Bills of Material
Other Uses for Bills of MaterialThe MRP Process
The MPS Grid
Steps in the Master Scheduling Process
Managing Change and the MPSCapacity Management
Types of Capacity
Capacity Planning Levels
Methods of Measuring Capacity
Capacity Required (Load)
Scheduling Techniques
Managing Overloads and UnderloadsClosed - Loop Planning
5. Operations Execution – Purchasing and Production Activity Control, APS
Purchasing
Purchasing versus Procurement
Relationship with Synchronized Plans
Purchasing Cycle
Current Functions and Trends
Environmentally Responsible Purchasing
Ethical Sourcing
Purchasing and Supply Chain Management
Purchasing Performance MeasurementsProduction Activity Control (PAC)
PAC Objectives and Functions
Types of Manufacturing
Data Requirements
Manufacturing Lead Time
Scheduling Techniques
Sequencing and Dispatching Orders
Bottleneck Management
Reporting and Performance MeasurementAdvanced Planning and Scheduling (APS)
What Is APS?
6. Distribution and Logistics Planning
The Role of Distribution in Supply Chain Management
Distribution Management in the Supply Chain
Distribution Planning and the Business PlanChannel Network Design
Importance of Good Channel Network Design
Channel Design Tree Structures
Insourcing or Outsourcing within the Channel Network
Labor and EquipmentInventory Planning
Balancing Supply and Demand
Distribution Channel Dependencies
Push or Pull?
Order (Reorder) Point
Basic Order–Point Model and Order–Point Trigger
Distribution Requirements Planning
Which to Use–Order Point or DRP?Warehousing
Function and Objectives of Warehousing
Strategic Decision Components
Warehouse Space and Capacity Planning
Types of Warehousing
Warehouse Automation and SystemsTransportation
The Transportation Function
Transportation Strategic Planning
Shipping Requirements
Track and TraceInformation Systems
Enterprise Resources Planning
Trace-and-Track Technology
-
Who is the course aimed at
READ THE DETAILS ▾
- Planning and Demand Management professionals
- Master Planners and Master Production Schedulers
- Production Schedulers
- Recently appointed Planning, Production and Logistics Managers and staff resources.
- Managers and staff resources from other plant functions who wants to improve their knowledge on Supply Chain Management and Manufacturing Planning & Control process (S&OP, MPS, MRP and PAC)
- ERP consultants
- Operations and Supply Chain Management Consultants
-
Pricing and enrolment
READ THE DETAILS ▾
ENROLMENT FEE
Contact us to know the price of the course: Email: info@advanceschool.ch
To register, you must send the completed registration form via email to info@advanceschool.ch, together with the receipt of the bank transfer or a purchase order.
The form can be downloaded from the link: Registration form